In the realm of industrial finishing, Powder Coating Machines stand as the bedrock upon which high - quality, durable coatings are erected. Whether you are a small - scale manufacturer treading the path of precision or a large - scale industrial behemoth dominating the production landscape, fathoming these machines is nothing short of essential for the triumph of powder coating operations.
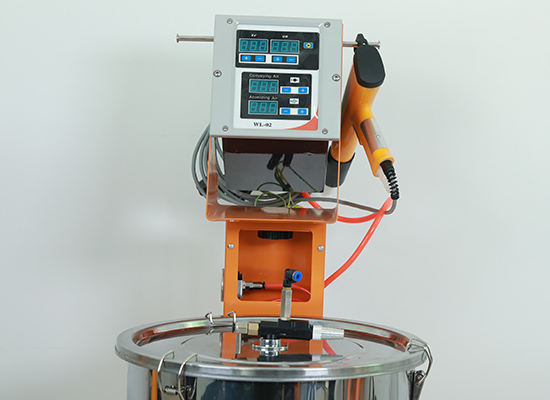
A
Powder Coating Machine is a veritable marvel of engineering, a sophisticated contraption meticulously designed to bestow a dry powder coating upon a diverse array of workpieces. It typically comprises several pivotal components: a powder - feeding system, a spray gun, an electrostatic charging unit, and a control panel.
The powder - feeding system serves as the repository for the powder coating material, dutifully supplying it to the spray gun. It can be classified into two main types: gravity - fed and pressure - fed. Gravity - fed systems, in their simplicity, rely on the immutable force of gravity to propel the powder, while pressure - fed systems harness the power of compressed air to thrust the powder towards the gun, thereby enabling more precise regulation of the powder flow.
The spray gun is the locus where the powder is artfully dispersed onto the workpiece. It comes in a variety of forms, such as manual and automatic guns. Manual guns, with their dexterity, are well - suited for small - scale projects or tasks demanding intricate detail, while automatic guns, with their efficiency, are the go - to choice for high - volume production.
The electrostatic charging unit is an indispensable part of the machine. As the powder courses through the gun, it imparts an electric charge to it. This charged powder is then magnetically attracted to the grounded workpiece, ensuring a uniform and tenacious coating.
The control panel serves as the operator's gateway to the machine, allowing for the adjustment of various parameters, including powder - flow rate, electrostatic voltage, and air pressure, to optimize the coating process.
Powder Coating Machines find their applications spanning a vast spectrum of industries. In the automotive industry, they are employed to adorn car bodies, engine components, and wheels. The powder coating not only provides exceptional corrosion resistance but also imparts a sleek, long - lasting finish.
In the furniture manufacturing sector, metal furniture frames and parts are cloaked in the protective and aesthetically pleasing embrace of powder coating. This not only elevates the visual allure of the furniture but also endows it with enhanced durability and scratch resistance.
The construction industry, too, reaps the benefits of powder coating machines. Metal building components such as window frames, handrails, and roofing sheets are coated to shield them from the ravages of the elements and enhance their aesthetic appeal.
The price of a
Powder Coating Machine can fluctuate markedly, contingent upon its features, capacity, and quality. A basic, entry - level machine, suitable for small - scale workshops or hobbyists, may command a price in the range of $500 - $1500. These machines typically possess straightforward functions and a rudimentary powder - feeding system.
Mid - range machines, equipped with more advanced features such as adjustable powder - flow control, superior electrostatic performance, and a more robust construction, generally carry a price tag between $2000 - $5000.
High - end industrial - grade machines, outfitted with automated powder - reclaim systems, high - precision control panels, and large - capacity powder - feeding systems, can cost upwards of $10000.
Prior to operating the machine, ensure proper grounding to forestall electrical mishaps. Connect all components in strict accordance with the manufacturer's instructions. Prime the powder - feeding system with the appropriate powder.
Adjust the powder - flow rate in consonance with the size and shape of the workpiece. For larger workpieces, a higher powder - flow rate may be requisite. Set the electrostatic voltage based on the type of powder and the desired coating thickness.
When spraying, hold the gun perpendicular to the workpiece and move it at a consistent pace. Maintain a distance of approximately 15 - 20 cm between the gun and the workpiece for optimal outcomes.
When embarking on the journey of choosing a
Powder Coating Machine, take into account your production volume. For high - volume production, an industrial - grade machine replete with advanced features is indispensable. For small - scale production or hobbyist use, a basic or mid - range machine will likely suffice.
Also, factor in the types of materials you intend to coat. Different materials may necessitate different electrostatic settings and powder - flow rates. Your budget is yet another crucial determinant. Strike a balance between your requirements and the cost to unearth the most suitable machine.
Safety assumes paramount importance when using a
Powder Coating Machine. Adorn yourself with appropriate personal protective equipment (PPE), including a dust mask to ward off the inhalation of powder particles, safety goggles to safeguard your eyes, and gloves to protect your hands.
Operate in a well - ventilated area to avert the accumulation of powder in the air, which can pose a fire or explosion hazard. Abstain from touching the electrostatic parts of the machine while it is in operation.
The design of a
Powder Coating Machine is a paragon of rationality. The electrostatic charging mechanism ensures efficient powder adhesion, thereby minimizing powder waste. The adjustable powder - flow and spray - pattern settings afford the flexibility to customize according to different workpiece shapes and sizes.
The utilization of high - quality materials in the construction of the machine guarantees its long - term reliability and performance. The control panel offers user - friendly operation, empowering operators to optimize the coating process.
Q: What should I do if the powder coating has an uneven thickness?
A: Scrutinize the powder - flow rate and the electrostatic charge settings. An erratic powder - flow rate or incorrect electrostatic charge can give rise to uneven coating. Additionally, ensure that the gun movement is steady and at the appropriate speed.
Q: Can I use different types of powder in the same machine?
A: Yes, but it is imperative to cleanse the powder - feeding system thoroughly between different powder types. Different powders may have disparate particle sizes and chemical compositions, which can impinge on the coating quality.
Q: How often should I maintain the electrostatic charging unit?
A: Conduct a monthly inspection of the electrostatic charging unit. Check for any loose connections or signs of wear. Perform a comprehensive maintenance every 6 - 12 months, encompassing cleaning and the replacement of worn - out parts.
Q: What if the powder doesn't spray out smoothly?
A: Inspect the powder - feeding system for any blockages. Also, ensure that the air pressure (if it's an air - assisted system) is stable. Clean or replace the gun nozzle if it is soiled or damaged.
Q: Can I upgrade my existing powder coating machine?
A: In certain instances, yes. You can upgrade components such as the powder - feeding system, the electrostatic charging unit, or the control panel. However, ensure that the new components are compatible with your existing machine.
Disclaimer: Enhance your coating process with advanced electrostatic powder coating machines, precision powder coating spray guns, comprehensive powder coating systems, and efficient powder coating lines from Hangzhou Huaxiang Coating Equipment Co., Ltd. Designed for reliability and high-quality finishes, our solutions meet all your industrial powder coating machine needs. Contact us at sale3@cncolourspray.com